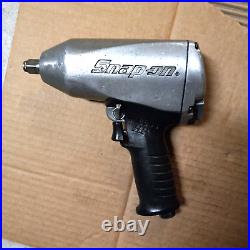
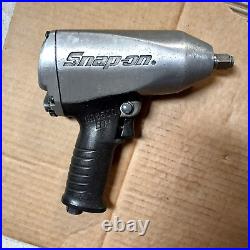
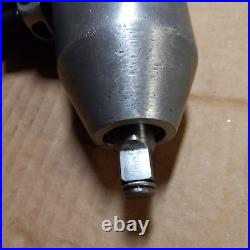
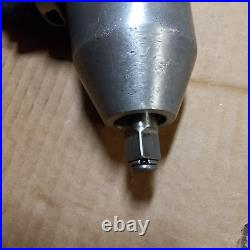
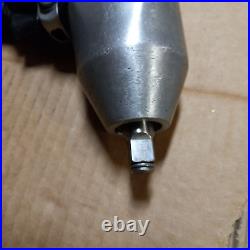
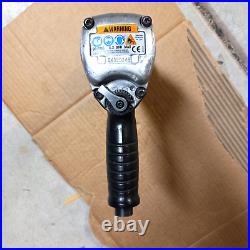
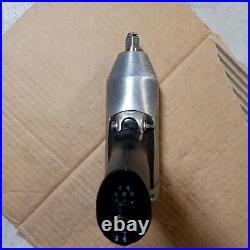
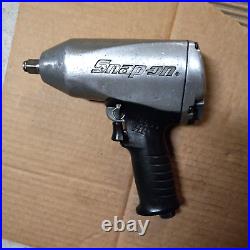
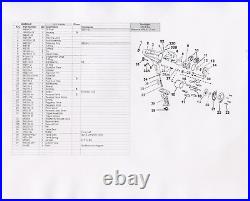

Offered for sale herein is a fully rebuilt IM6100 that was restored and now upgraded from the Snap On IM6100 1/2 drive model to a Snap On IM6500HP tool. This air wrench was bought as a used working tool needing a tune up. I performed the complete teardown, inspection, made necessary parts replacement and upgraded this tool to much-better-than-new-performance. The IM6100 was originally made as a 6-vane grooved rotor design. It was good for about 460 foot pounds. The tool was reliable but gave way to the IM6500HP which offered an 8-vane groove rotor. The older: hammer frame, anvil, hammers and hammer pins were much better parts than the newer PT850 and older MG725 tools were engineered to use. This tool has a new 8-vane groove rotor which updates this tool to perform as well as a new PT850 or older model MG725. This IM6500HP was Snap On test torque rated for 690 foot pounds back when the Snap On service centers repaired this tool over 13 years ago. This actual number is closer to a range of 700 to 800 maximum foot pounds (with high volume air fittings and air pressure between 90 to 100 psi on full open throttle operation). Used properly in daily repair work and avoiding heavy and long impacting duty cycles on frozen rusted fasteners (for longer than 3 to 5 seconds) will allow this tool to operate for 10 to 20 years or more. Simply breaking loose rusty and frozen fasteners using a breaker bar and penetrating oil will allow this tool to last 20 years. This tool is often preferred by older mechanics who began their career over 20 years ago. I installed an updated reverse valve kit (for better sealing and internal air flow) with a quad ring spool seal and a new back cover gasket. I surfaced the back cover for a parallel condition making a positive air seal. The clean and used impact mechanism parts will assure long service life from this tool to an appreciative end user. I also installed a new Snap On IM6500HP tool handle grip. The grip is obsolete from Snap On. It confirms that the tool is the model I claim it to be. I spend a great deal of time hand polishing the internal surfaces of the tool housing so that I can install dry parts without any drag or friction. I have found that this is a key to proper Snap On impact wrench repairs. Removing drag by hand polishing and metal surface smoothing then using dry parts to test fitment before making final assembly easy assures final assembly and tool operation that will provide like-new performance. Many new Snap On tools are built with new parts that are not properly fit well to each other. It is often overlooked on remediation by service technicians who force the same poorly fitting parts back together only to create internal binding. New o’rings, oil seals, Snap On rotor vanes and Chinese bearings (Snap On also uses them) complete the parts I change out. Air motor end plates are resurfaced, then properly cleaned and inspected for fit and fitment. This will make smooth installation without burrs and nicks that cause internal scuffing and drag marks to the tool housing. I typically hone my cylinders and scrap any parts that are micro cracked or rust pitted. The air motor is never given short shrift in my repairs as this is where the tool develops rotor drive end rpm. With this deal I also provide (2) extra 1/2 anvil retaining ring kits. Dirty and wet air will be the death any Snap On air wrench. Daily oiling and or an inline oiling and filtration system will give many excellent years of forward service life to this tool. This IM6500HP tool was uniquely designed to allow exhaust air to freely pass forward by operating the bypass lever and or to act quietly by routing the exhaust air down the tool handle and out through a sound dampener. The problem with the noise dampener was that it became impacted with dirt and grit over time so it then became a choke point. I change that noise dampener out with a smaller sized filter with large open pores to let the tool breathe. I also install the later designed new style forward and reverse valve and seal the valve stem with a quad ring. The reverse valve stem on these Snap On 3100, 5100, 6100 and 6500HP series was notorious for stem leaks. The 8-vane rotor design with reduced exhaust air restriction is what this tool now is about. There are no marginal parts being used in this rebuild. I do recommend using 2 or 3 wraps of plumbers teflon tape on the last few threads (but not on the first 2 threads) of your male threaded shop air fitting to avoid bottoming into the inlet bushing threads with your shop air fitting to capture a proper air seal. Teflon tape can shred and clog the bushing debris screen when not carefully used. Avoid using air fittings with less than 1/4 ID and make sure to obtain 90 psi air pressure to the tool with air hoses that are not cracked internally. If you have any performance problems with any air tool always check the air inlet bushing debris screen first to make sure that the tool is not being starved for air supply. That is because there are some shops with wet and dirty air, deteriorating air hoses or shop air piping that will destroy tools. If you do have a tool performance issue that is my fault I recognize that you will need my support to make corrective repairs. I make every effort to correct any existing tool issues and verify my work when I rebuild a pneumatic tool.
